
Discover how advanced automated storage solutions are addressing the complexities of pharmaceutical inventory management.
Introduction:
The pharmaceutical industry is a nexus of complexity and stringent regulations. Managing inventory in this environment is not just challenging—it’s critical. As pharmaceutical companies seek to optimize their logistics and reduce costs without compromising on quality, the adoption of advanced, automated storage solutions is becoming increasingly prevalent.
What can be stored in Modula VLMs?
Pharmaceutical companies face a unique set of challenges that can significantly impact operational efficiency. These include strict regulatory compliance, the need for product traceability, temperature-sensitive medication integrity, and accurate demand forecasting to prevent stockouts or overstocking, etc.
The Healthcare Distribution Alliance (HDA) reports that inventory mismanagement can lead to a 1-3% annual sales loss. Key issues include:
- Regulatory Compliance: The medical industry has strict regulatory requirements for the storage of drugs and medical devices, such as GMP (Good Manufacturing Practice) and GDP (Good Distribution Practice), which must be adhered to. The warehouse team needs regular training to stay informed about the latest regulations, procedures, and technologies.
- Environmental Control: Many pharmaceuticals and medical devices are sensitive to storage conditions like temperature, humidity, and light exposure, necessitating precise environmental control. Specific conditions are vital for maintaining the potency of medicines and vaccines. Cross-contamination can degrade drug efficacy and alter properties.
- Traceability: High-value items like medical equipment require robust security measures to prevent theft. Accurate tracking across a wide range of products is essential for efficient operations. There is a need for a comprehensive traceability system for medical products, ensuring safety and accountability from production to the end-user.
- Inventory Management: Managing the inventory of medical products is complex, requiring real-time monitoring to prevent expiration and waste, while ensuring the availability of critical supplies.
- Security Management: Rigorous security measures are essential, covering both physical security to prevent theft and unauthorized access, and data security to protect patient and product information.
- Disposal of Expired Products: Safe and compliant disposal of expired drugs and medical devices involves strict procedures and documentation.
- Supply Chain Coordination: The medical supply chain is intricate, requiring coordination with suppliers, manufacturers, hospitals, and patients to ensure efficient operation.
- Technological Challenges: With technological advancements, medical warehouses need to continuously update and upgrade their management systems, potentially incorporating automated and intelligent storage solutions.
- Cost Control: Balancing compliance and safety with cost control is a challenge, considering expenses related to labor, equipment, and utilities.
- Emergency Preparedness: Medical warehouses must have contingency plans for emergencies such as natural disasters or pandemics to ensure rapid deployment of critical medical supplies.
- Order Service: High-quality order handling is essential, including rapid response times, accurate delivery, and excellent after-sales support.
Digital Transformation in Pharmaceutical Storage
In response to these challenges, there is a shift towards digital solutions that promise to save space, enhance productivity, and ensure accuracy in inventory management, leading to cost reductions.
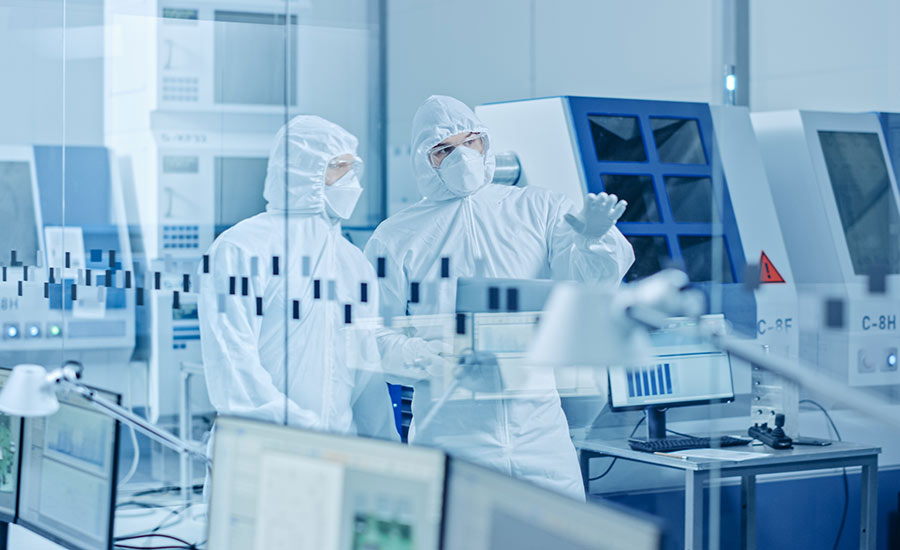
Automated Solutions
The Benefits of Automated Storage in Pharmaceuticals:
Automated storage solutions, such as Modula’s vertical lift modules (VLMs), are being adopted across the globe to address these challenges:
Climate Control: Modula’s VLMs regulate temperature and humidity, ensuring the safety and efficacy of stored medications.
Clean Room Compliance: The Modula Clean Room system prevents contamination and meets ISO standards.
Security: Automated systems feature secure access control, protecting against unauthorized access.
Maximizing Efficiency and Safety:
Space Efficiency: Saving up to 90% of floor space compared to traditional storage.
Productivity and Accuracy: Streamlined picking and replenishment processes.
Ergonomic Design: Items are retrieved at ergonomic heights, enhancing worker safety.
Real-Time Inventory Management: Full traceability and real-time tracking of stock levels.
Integration and Traceability:
Modula’s warehouse management system (WMS) integrates seamlessly with existing ERP, SAP and many other systems, providing a unified platform for inventory control and reducing the risk of human error.
Real-World Success Stories:
Innomed (USA): Innomed was facing space constraints, the only space they could utilize is vertical space. Following a comprehensive review, the company has installed 4 Modula VLMs. The four units now provide over 92.2 cubic meters of storage capacity within a 57 square meter area, enabling the company to store over 8,500 medical instruments. “It was surprising to us that we could store 90% of our inventory in the machine,” says Aaron Ingram, Vice President of Product Operations.
With 9% of their surgical instruments stored in one central area, the picking and replenishment process became streamlined and efficient. Operators are no longer required to climb ladders and navigate multiple areas to fulfil multiple lines orders. The Modula VLM enables operators to retrieve all items from a single location, ensuring ergonomic access, safety and ease of use.
Santé Service (France): Sante Service selected two Modula Lift ML25 VLMs to enhance picking speed and accuracy when handling medical supplies. The VLMs enabled the organization to achieve quick and error-free picking. Radiofrequency terminals are used to send orders for medical supplies to the Modula VLMs, which then prepare them. Once the items have been retrieved, operators place them in containers with clear guidance from a laser indicator. The containers are then conveyed to the various departments via conveyor belts. Sante Service opted for a double, opposed bay configuration, which allows access to the machine from two positions. This configuration allows two operators to perform picking and transfer operations simultaneously. The Modula VLM also made the most efficient use of vertical space, with parts previously stored on 225 square meter shelves now fitting into machines that occupy just 15 square meters of floor space.
Orfit Industries (Belgium): Orfit first encountered Modula at a local exhibition in Belgium, where they were impressed by the performance of Modula VLMs. In order to accurately manage a large number of orders and optimise warehouse space, Orfit purchased 7 Modula VLMs and put them into use immediately.
Without adding additional operators, the Modula VLM demonstrated the advantages of saving space, increasing efficiency and improving accuracy.
The picking efficiency alone has increased by nearly 6 times. Prior to the introduction of the Modula VLM, the average order quantity processed manually was 40 pieces per hour. Following the implementation of the Modula VLM, this figure has increased to 220 pieces per hour.
Conclusion:
Automated storage solutions are revolutionizing pharmaceutical intralogistics, offering a strategic advantage in a highly regulated sector. Modula’s advanced systems are designed to optimize operations, ensuring precision, safety, and efficiency.
Ready to transform your pharmaceutical facility with cutting-edge storage technology? Contact Modula for a comprehensive warehouse audit and discover how our solutions can enhance your productivity and efficiency.