Over the last four years, Modula China factory has achieved considerable success, and since 2022, we have become a leader in the automated vertical storage industry within China and globally. The rapid sales growth has driven the optimization and innovation of supply chain management (SCM).
We interviewed Mr. Frank Wu, the Supply Chain Manager of Modula China, and discussed how the supply chain is organized at Modula China. We also discussed how Modula improves the quality of its products and services, and how it builds its core competitiveness.
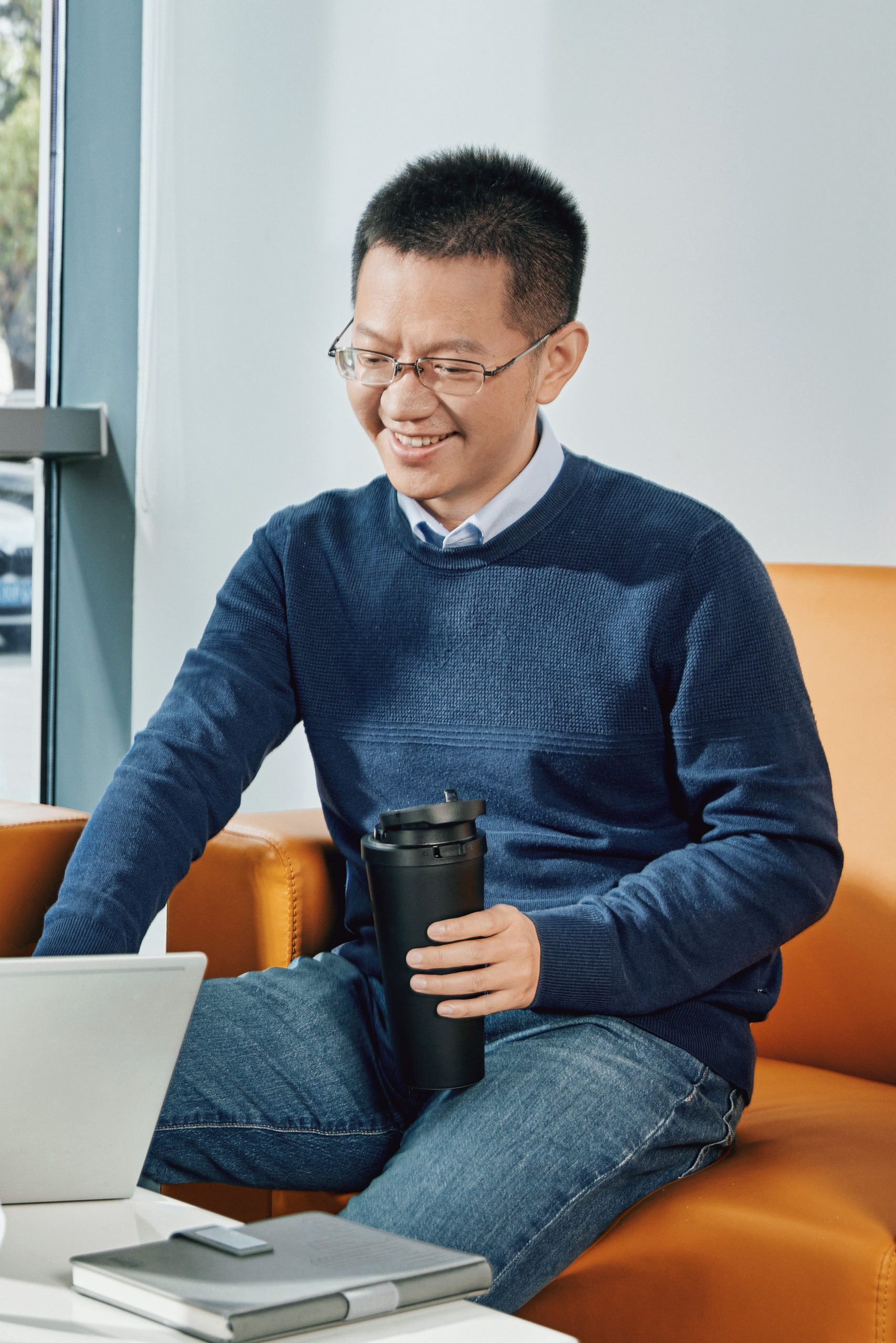
“Logistics Tech Outlook” conducted an exclusive interview with Mr. Miguel A. Fabra, Managing Director of Modula APAC, and deeply analyzed Modula’s product advantages and application cases of warehouse management solutions.
What is Supply Chain? What is the difference between Supply Chain and Logistics?
The supply chain is a complex but essential concept that entails procurement, production, packaging, and shipping processes necessary for the company’s operations.
The term ‘Supply Chain’ is often confused with logistics, which is a narrower concept that primarily deals with the transport of goods from one point to another while keeping the costs optimal and ensuring high-quality and efficient transportation.
What is supply chain management and what sectors does it affect?
Supply chain management can be summarized by the 8 Rs: using the correct method to deliver the right products to the right place, at the right time, with the right quantity, quality, and condition, in order to optimize costs. Using Modula’s business model as an example, supply chain management includes procurement, planning, warehousing, logistics management, and more.
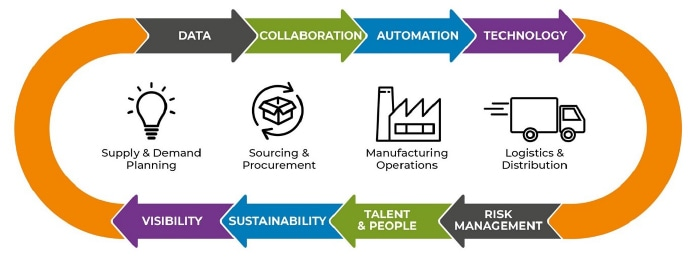
The entire supply chain is connected via the flow of products, information, and capital. Product flow commences with raw material procurement, manufacturing, assembling, and packaging of finished goods. It forms the basis of all other flows, and for every stage of product flow, there is a corresponding information flow which the ERP system must track and update precisely to ensure cash flow is accurately recorded.
For instance, when a parcel is dispatched, the recipient’s name, address, and phone number are recorded, and this represents the information flow. Every stage involved in the process is interrelated with cash flow. Cash flow originates from customer prepayments and drives the entire capital flow. This flows in the opposite direction to the product flow.
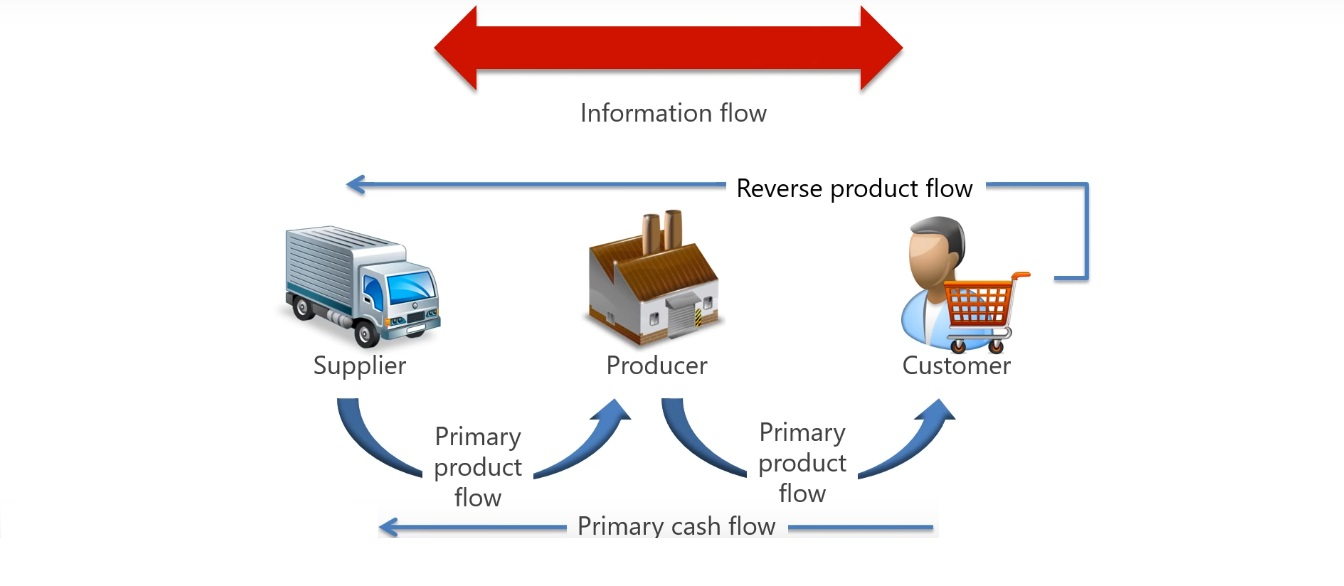
What is supply chain management and what sectors does it affect?
Supply chain managers are responsible for developing and continuously optimizing supply chain management processes, managing daily operations and suppliers, with the goal of reducing costs and enhancing operational efficiency for the company.
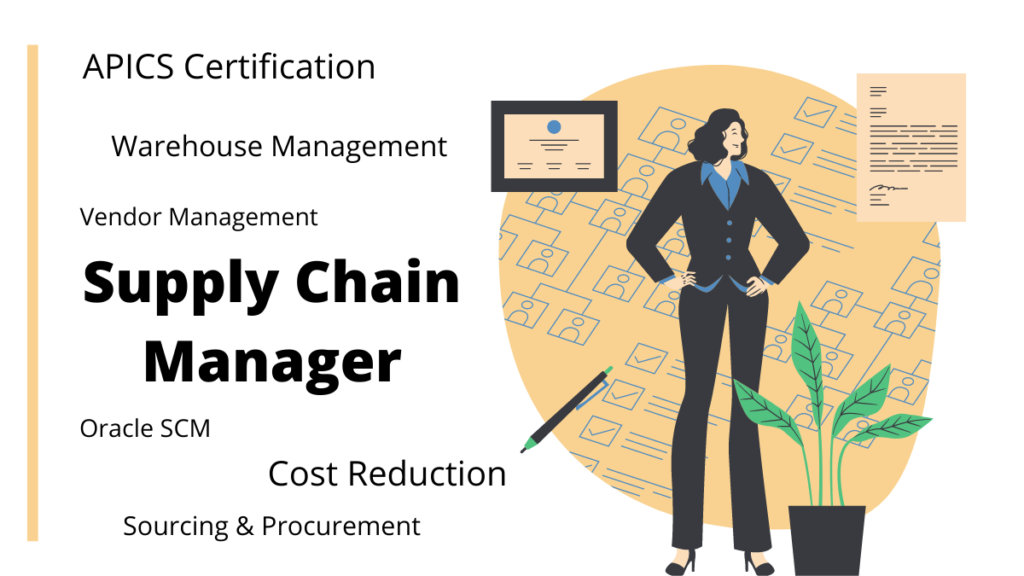
Supply chain managers should consider the indicators for the entire supply chain, such as inventory turnover rate and on-time delivery rate. Departments that are responsible for these indicators typically prioritize the best performance of their own department over the performance or impact of other departments. Therefore, supply chain managers must coordinate these departments to achieve the overall optimal solution and make the most favorable decision for the company.
What equipment does a Supply Chain require?
The most commonly used hardware in supply chain management consists mainly of storage and logistics equipment, including wrapping machines, forklifts, pallet jacks and Modula automated vertical warehouses, as well as AS/RS (Automated Storage and Retrieval Systems).
There are many software applications in supply chain management, with the MM module (material management) and PP module (production planning) being frequently used in the SAP system. The technical department uses software for loading and optimizing finished product deliveries, 3D modeling, and kitting list preparation. The planning department widely uses MPS (Modula Production System), TeM (Tempi e Metodi), and warehouse management systems (WMS), among others. At Modula, we continually develop more sophisticated software and enable them to communicate and work together to support our operations.
For example, Modula offers customizable configurations for their automated vertical lift modules. There are thousands of possible combinations of machine height, width, tray width, tray depth, tray wall height, payload, and options. Using traditional methods to create a Bill of Materials and calculate costs can take days or even months for design, engineering, procurement, and other relevant departments to complete. Using software and information technology, sales can independently create offers in the system after the customer selects the model and options. This allows for instant access to information such as list prices and discounts of the machine.
The entire supply chain has been digitized and is coordinated through an intelligent information system. Thanks to this technology, the supply chain department is streamlined, resulting in enhanced work efficiency. We are not only adopting Industry 4.0 practices but also Supply Chain 4.0 strategies.
How is the supply chain organized at Modula China?
Modula China’s supply chain has two primary objectives: maximizing customer value and minimizing supply chain costs.
During Modula’s initial production in China, our supply chain heavily relied on our headquarters, leveraging the resources and bulk purchasing power of the central office.
Sales growth at our China factory and the impact of COVID on the global supply chain have necessitated a shift to localization. We have now integrated high-quality local suppliers into our complete supply chain in China. In 2022, we achieved 80% localization and are aiming to reach 90% in the near future.
There are many benefits of supply chain localization, firstly it can reduce the lead time of our orders and improve production efficiency. Second, it helps to optimize cost control, such as reducing various costs of purchasing from abroad, transportation, customs clearance, tariffs, etc.
In fact, localization helps us to stay competitive in the market, customers could enjoy our cost reduction as well as short lead time. To achieve fast delivery within four weeks, even in unexpected emergencies, our supply chain localization plays an essential role, we can be much more flexible than companies that rely on foreign supply chains.
In terms of after-sales service capabilities, supply chain localization allows us to have efficient spare parts, instead of urgently transferring goods from abroad, which will increase communication costs and downtime risks for customers, we deliver directly from China in a very short time at a reasonable cost, which has greatly improved customer satisfaction.
The differences of the supply chain management between Modula China and headquarters
The supply chain management of Modula China and the headquarters are different, the annual output of the head office is more than 3,000 units, more software systems are used to support the whole manufacturing process, such as TeM (Tempi e Metodi), etc. Even with the same software, the headquarters need to develop more functions, such as MPS (Modula Production System) software, China is using the basic functions for now, with the production growing year by year, we will catch up very soon.

ITALY Headquarters – Salvaterra (RE)
Meanwhile, China’s supply chain department and our headquarters work closely together, China receives strong support from headquarters. For example, during the COVID shutdown, when many local suppliers were unable to deliver on time, our head office had sufficient stocks and prepared all the materials and sent them by air to support our production to ensure that the Suzhou factory could meet its commitment to customers.
In addition, our localization has also received strong support from headquarters. When selecting local suppliers, head office has shared a lot of experiences and supplier resources, helping us to reduce trial and error costs, find high-quality suppliers and speed up the localization process.
As a foreign automated storage solution brand with manufacturing in China, Modula is always customer-oriented, we constantly improve the efficiency of the supply chain to remain the market leader.
In the long run, Modula China will continue to strengthen the supply chain system, accelerate the localization strategy, radiate the supply chain network across the country to provide customers with better products, more professional and efficient services.
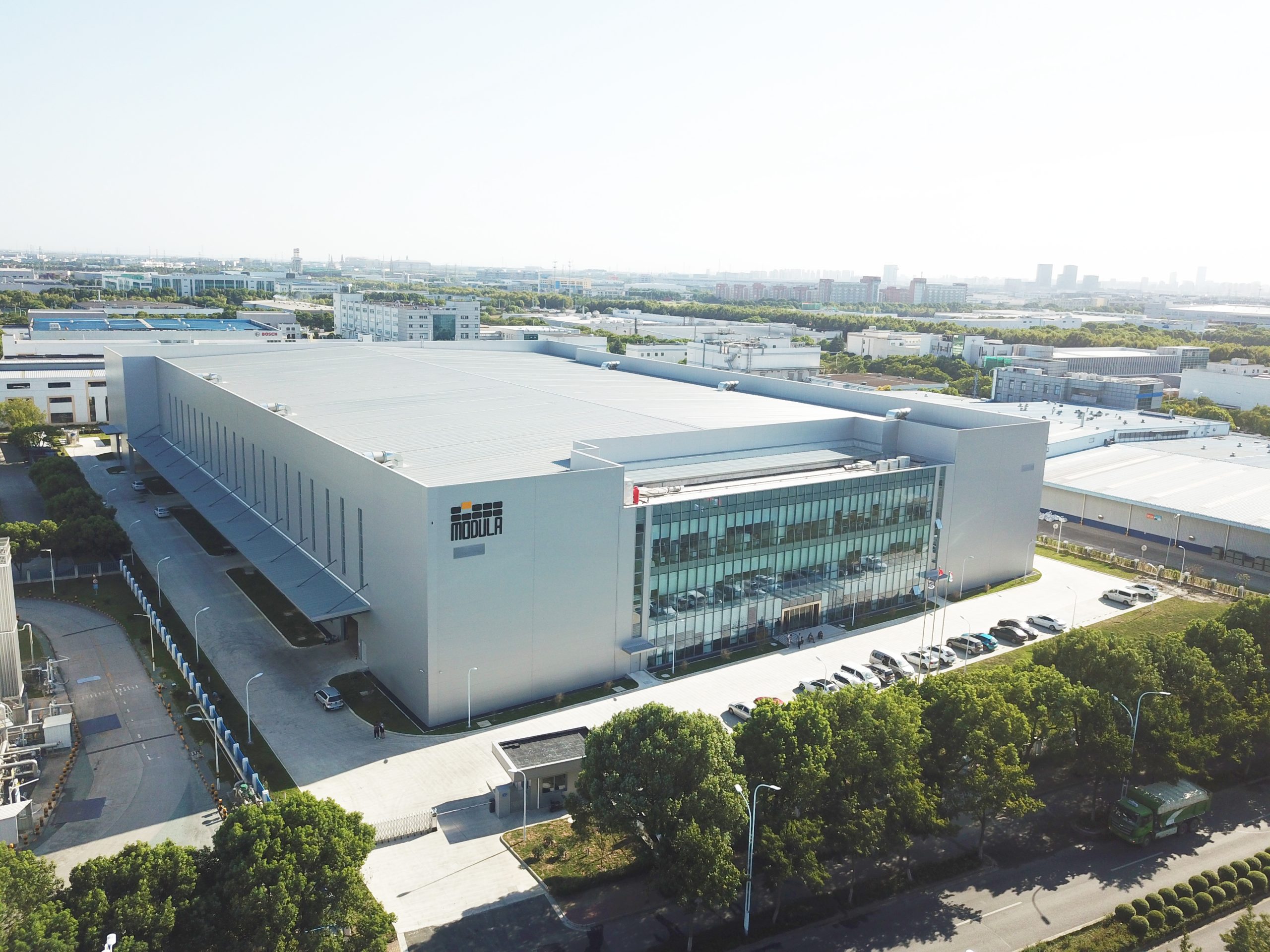
Modula China