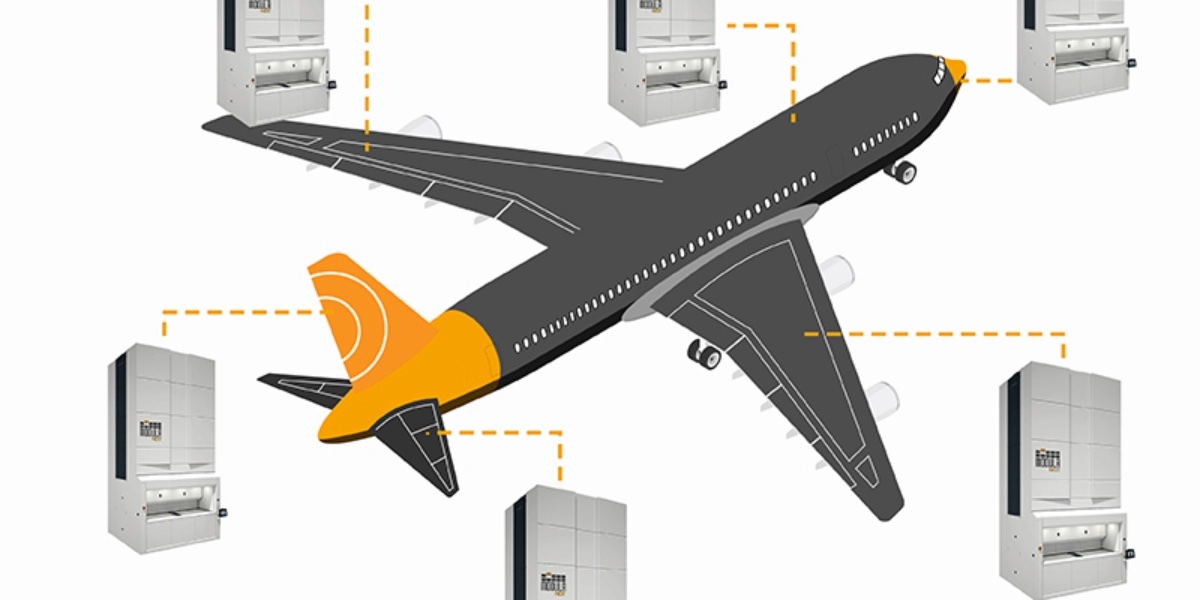
The Aerospace & Defense industry has demonstrated remarkable resilience in the face of the challenges posed by the COVID-19 pandemic. Despite significant challenges, it has swiftly rebounded and is on track to return to pre-pandemic levels by 2024. As the industry adjusts to new market dynamics, including fleet upgrades, digital transformation, and emissions reduction targets, optimizing productivity and efficiency has become a top priority as well.
In the realm of Maintenance, Repair, and Operations (MRO), challenges persist due to staff shortages, economic uncertainty, geographic conflicts, and fuel price fluctuations, disrupting the aerospace supply chain. To mitigate these challenges, industry leaders are bolstering their stocks and investing in regional infrastructure to reduce waiting times.
In this context, optimizing logistics becomes increasingly crucial for the Aerospace & Defense sector’s development. Modula’s cutting-edge vertical and modular solutions have become a key enabler of enhanced logistics processes, trusted by top industry players worldwide.
Modula’s solutions streamline logistics operations, optimizing storage space, reducing picking times and enhancing operational accuracy. Modula has a proven track record of success in addressing critical challenges and driving improvements effectively, as evidenced by its work with industry giants such as Safran, Airbus, China Eastern airlines, China Sichuan airlines, Lufthansa and the US Navy.
Modula’s Vertical Lift Modules (VLMs) provide tailored solutions for the Aerospace & Defense sector, ensuring total traceability of materials and facilitating faster, more precise picking.
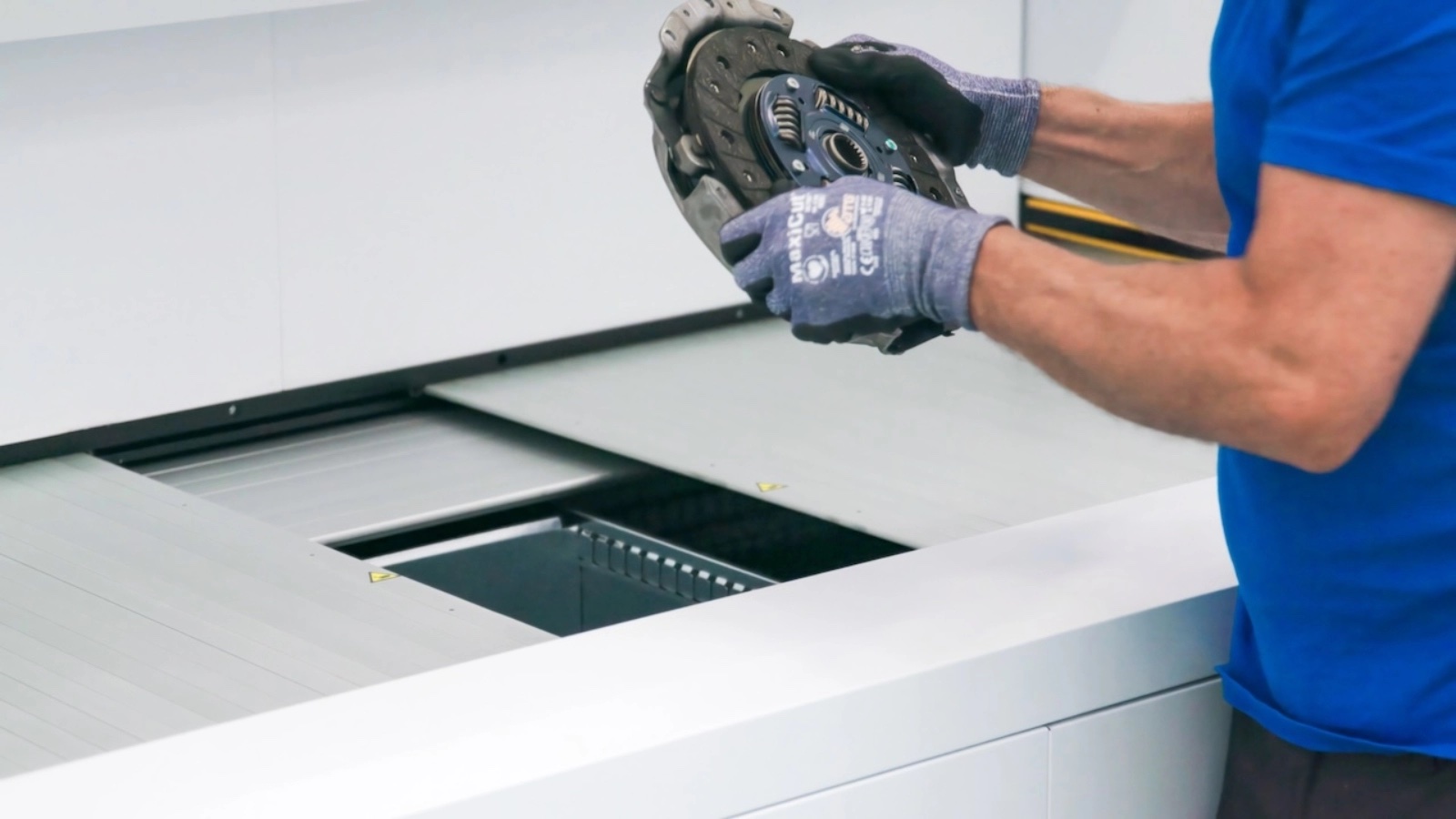
What can be stored in Modula VLMs?
Any type of parts can be stored in the Modula VLMs. Such as Aircraft and airport ground support equipment (GSE)
- Safety stock for all highly critical parts and components
- Delicate materials and composites that need protected or temp controlled storage
- Motors and batteries
- Position lights and signaling components
- Flight instrumentation
- Tool Cribs
- Spare engine parts, kits, gaskets, tires
- Fuel and emissions systems.
- Cables, internal wiring, electrical and electronic components
The size of the products and tooling in question present ergonomic and space claim challenges. The aerospace industry requires a significant number of parts and components in a wide range of sizes and weights, often on short notice. It is important to store and organize small and fragile components in an efficient manner to ensure they are easily and quickly accessible. It is essential that large and heavy parts are picked and lifted at the optimal working height to guarantee the safety of both the products and the operators.
The innovative Modula NEXT system represents an upgrade of the Modula VLM., designed for the storage and picking of large quantities of similar items, features dedicated access and a vending machine-style sliding window system; ensuring accurate retrieval and eliminating risk.
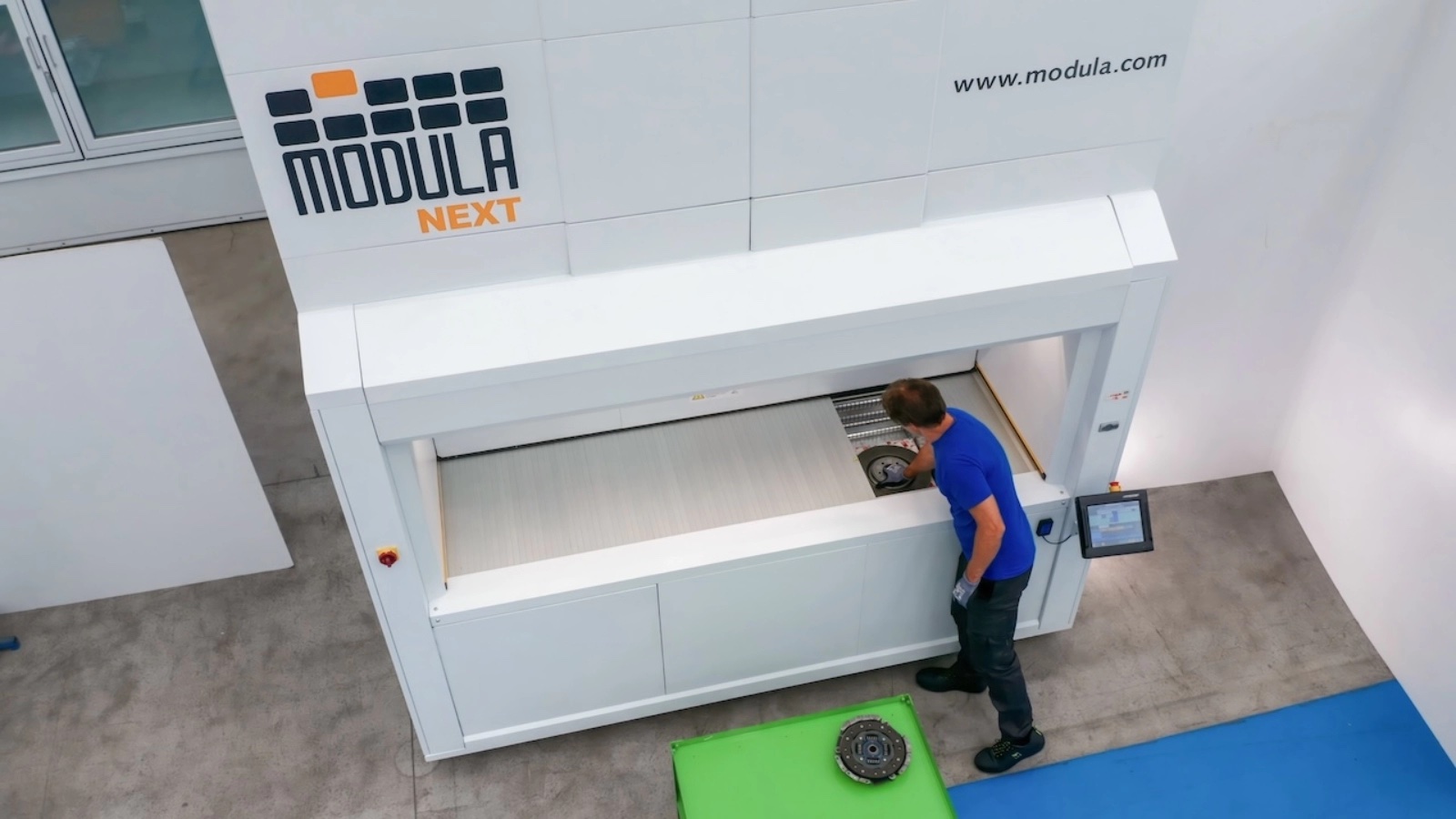
How does Modula NEXT work?
Modula NEXT is an automated warehouse storage solution that combines the precision and control of industrial vending machines with the space-saving and efficiency-enhancing features of VLMs. It is an ideal solution for maximizing your existing floor area, as it only occupies 9 sqm of your floor space. Furthermore, it is an affordable option that can help you cut costs, since land is getting more and more expensive.
Modula NEXT’s customizable compartments allow it to accommodate products of different shapes and sizes, a feature uncommon in traditional vending machines which typically have fixed compartment sizes. Its adaptability makes it ideal for a wide range of industries and items, from small parts to larger tools and components.
Modula NEXT offers operational versatility, enabling users to operate it as a traditional vending machine or a VLM. This versatility allows it to meet different needs, from strict inventory management to quick bulk access, all in one system.
This compatibility to different software allows Modula NEXT to integrate into advanced systems, such as SAP, ERP, etc. Providing businesses with a scalable and flexible storage option.
Modula WMS can cover these needs through specific functions:
- Management of production batches, serial numbers, and serial numbers
- Management of production date and expiry date
- FIFO management
- Tray access limitation depending on user account.
- Active Directory Authentication: use user, domain and password defined in active directory
- Advanced user management; configuration of enabled procedures for each individual user
- Manual or on-demand inventories from the company ERP
All product input and output operations are tracked and stored in the Modula WMS history that can be consulted via WMS client or exported to the ERP via file, ODBC or Webservice.
Furthermore, Modula products offer a superior tracking precision compared to traditional shelves, enabling comprehensive inventory control, and mitigating the risks of understocking and overstocking. The optimised tracking system ensures safe and controlled material management, maximizing precision in every intralogistics stage.
By utilizing the advanced functions of Modula products, companies in the aerospace and defense industry can significantly enhance operational efficiency while maintaining exceptional performance levels and competitiveness in the global market.
For further details on Modula’s pioneering solutions and technology, please do not hesitate to contact us for individually tailored technical advice.